Understanding the Art of Manufacturing 3-inch Flanged Butterfly Valves A Comprehensive Guide
In the world of industrial fluid control systems, the 3-inch flanged butterfly valve stands as a critical component, offering an efficient and cost-effective solution for managing flow rates. This article delves into the intricacies of the manufacturers behind these high-performance valves, exploring their craftsmanship, technology, and dedication to precision engineering.
A 3-inch flanged butterfly valve is designed to regulate the flow of fluids in pipelines with a diameter of 3 inches. The valve's distinct feature, the butterfly disc, pivots on a central shaft, allowing for quick opening and closing actions. The flanges attached to both ends of the valve enable easy installation between pipeline flanges, making it a popular choice for various industries, from chemical processing to water treatment plants.
Manufacturers of 3-inch flanged butterfly valves are a specialized breed, combining technical expertise with innovative design principles. They employ advanced materials such as stainless steel, carbon steel, and, ensuring durability and resistance against corrosion. These materials are selected based on the specific application requirements, such as temperature, pressure ratings, and chemical compatibility.
The manufacturing process begins with computer-aided design (CAD) software, where engineers create detailed blueprints tailored to customer specifications. This is followed by Computer-Aided Manufacturing (CAM), where the digital designs are translated into precise machine instructions. High-tech CNC machines then take over, cutting and shaping the components with micron-level accuracy.
Quality control is paramount in this industry. Manufacturers rigorously test each valve at every stage of production, from raw material inspection to finished product assessment. Pressure testing, endurance testing, and leakage testing are standard procedures to ensure the valves meet international standards like API, ANSI, and DIN Pressure testing, endurance testing, and leakage testing are standard procedures to ensure the valves meet international standards like API, ANSI, and DIN
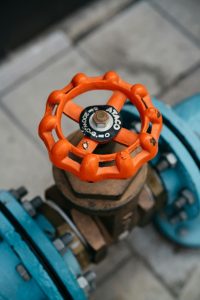
Pressure testing, endurance testing, and leakage testing are standard procedures to ensure the valves meet international standards like API, ANSI, and DIN Pressure testing, endurance testing, and leakage testing are standard procedures to ensure the valves meet international standards like API, ANSI, and DIN
3 inch flanged butterfly valve manufacturers.
Moreover, customization is a key aspect. Manufacturers understand that no two applications are alike and offer tailored solutions. This can range from different lining materials for chemical resistance to various actuation options, including manual, pneumatic, electric, or hydraulic.
Innovation is a driving force in the sector. Continuous research and development efforts lead to improvements in valve design, material science, and manufacturing processes. This not only enhances performance but also reduces maintenance costs and downtime for end-users.
The global market for 3-inch flanged butterfly valve manufacturers is competitive, with companies vying to deliver the best combination of quality, reliability, and value. Leading manufacturers, such as Emerson, Flowserve, and Metso, have established reputations for their robust products and exceptional service.
In conclusion, the manufacturers of 3-inch flanged butterfly valves are the architects of fluid control solutions. Their commitment to precision engineering, continuous innovation, and stringent quality control ensures that these valves play a pivotal role in numerous industrial operations worldwide. As technology advances and environmental concerns grow, these manufacturers will continue to shape the future of fluid management with smarter, more sustainable solutions.